Mastering Injection Moulding Tooling for Superior Metal Fabrication
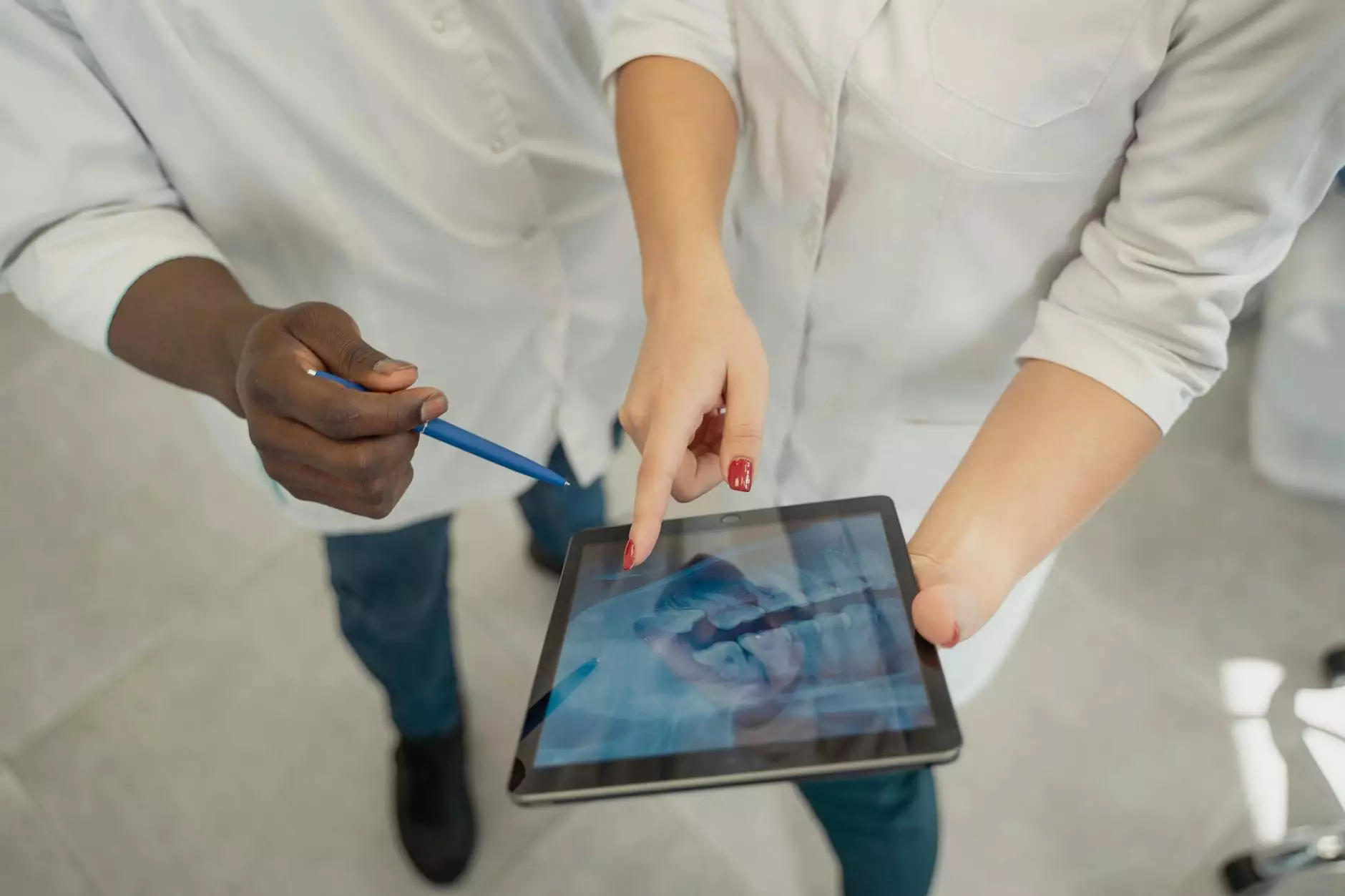
Injection moulding tooling has revolutionized the landscape of manufacturing, especially in the field of metal fabrication. This comprehensive guide delves into the intricate processes and techniques involved in injection moulding tooling, while emphasizing its significance for businesses aiming to enhance production efficiency and product quality.
Understanding Injection Moulding Tooling
To fully appreciate injection moulding tooling, it’s essential to grasp its foundational elements. At its core, injection moulding is a manufacturing process where molten material is injected into a mould cavity. Once cooled, the material hardens and takes on the shape of the mould. The tooling aspect refers to the design, construction, and maintenance of these moulds, which are vital for the successful production of high-quality parts.
The Components of Injection Moulding Tooling
Each injection moulding tool comprises several critical components:
- Mould Base: The base holds the mould together and supports the injection system.
- Mould Cavity: The hollow section where the molten material is injected and formed into shape.
- Mould Core: Typically used to create internal features within a part.
- Injection Nozzle: The part where molten material enters the mould cavity.
- Cooling Channels: These regulate the temperature of the mould to ensure proper cooling of the injected material.
The Advantages of Using Injection Moulding Tooling
The benefits of injection moulding tooling for businesses are extensive. Here are some important advantages:
- High Production Speed: Injection moulding allows for rapid production cycles, making it ideal for mass manufacturing.
- Consistency and Precision: Automated processes ensure that each part is produced to exact specifications, reducing errors and waste.
- Material Versatility: A wide range of materials can be used in injection moulding including metals, plastics, and composites.
- Cost-Effective for Large Runs: Although initial tooling costs can be high, the per-unit cost decreases significantly with large production runs.
Cost Factors in Injection Moulding Tooling
While the advantages are compelling, businesses must also consider the costs associated with injection moulding tooling. Key factors include:
- Tooling Design Complexity: More intricate designs require more sophisticated and often more expensive tooling.
- Material Selection: The choice of materials for the mould can impact costs significantly.
- Production Volume: Higher volumes can dilute tooling costs, making investment more attractive.
- Maintenance and Repairs: Regular maintenance can prevent additional costs due to wear and tear.
The Role of Deep Mould in Injection Moulding Tooling
As a leader in the metal fabricators category, Deep Mould is at the forefront of providing cutting-edge injection moulding tooling solutions. Our focus on innovation, quality, and customer satisfaction sets us apart from the competition. Here’s how we excel:
1. Expertise and Experience
With years of experience in the industry, our team is highly skilled in all aspects of injection moulding tooling. We stay updated on the latest trends and technologies, ensuring our clients receive the best solutions.
2. Advanced Technology and Equipment
Utilizing state-of-the-art machinery allows us to create precise moulds that meet the rigorous standards of modern manufacturing. Our investment in technology reflects our commitment to quality.
3. Tailored Solutions
We understand that every project is unique. Deep Mould offers customized tooling solutions that meet specific requirements, ensuring optimal performance and efficiency in production.
4. Quality Assurance
Quality is non-negotiable at Deep Mould. Our rigorous quality control processes guarantee that every tool we produce meets high standards, resulting in excellent end products for our clients.
Considerations for Successful Injection Moulding Production
To achieve the best results in injection moulding tooling, several factors should be considered:
- Material Properties: Understanding the physical and chemical properties of the material used for injection is crucial for optimally designing the mould.
- Design for Manufacturability (DFM): Parts need to be designed not just for functionality but also for manufacturability to minimize complexities in the production process.
- Cycle Time Optimization: Streamlining the cycle times through efficient design and process tweaks can vastly improve production output.
- Cooling Time Management: Effective cooling is essential to prevent defects and ensure the quality of the moulded parts.
Environmental Considerations in Injection Moulding Tooling
As businesses look to improve their environmental footprint, the role of injection moulding tooling plays an instrumental part. Here are several environmentally-friendly practices being adopted:
- Material Recycling: Many companies are now using recycled materials for the injection moulding process, reducing waste and conserving resources.
- Efficient Energy Use: Advanced machinery that requires less energy minimizes the carbon footprint associated with the production process.
- Reduced Material Waste: Precision in design and manufacturing processes ensures that less material is wasted.
Future Trends in Injection Moulding Tooling
The world of injection moulding tooling is continually evolving. Significant trends that businesses should keep an eye on include:
- Automation and Smart Manufacturing: The rise of automation technologies is set to enhance production efficiency and reduce manual errors.
- 3D Printing in Tooling: The use of additive manufacturing technologies is becoming more common for creating complex mould designs.
- Integration of IoT: The Internet of Things is paving the way for smart industry solutions, allowing moulds to be monitored and managed remotely.
- Focus on Sustainability: Companies are increasingly seeking sustainable practices that reduce environmental impacts in their manufacturing processes.
Conclusion
In conclusion, injection moulding tooling is a pivotal component in the realm of manufacturing, particularly in the field of metal fabricators. Understanding its intricacies can empower businesses to optimize their production processes and enhance product quality. Deep Mould stands ready to guide and provide innovative solutions tailored to the unique needs of each client. When you choose Deep Mould, you're not just selecting a service provider; you're partnering with a leader dedicated to excellence, sustainability, and advancing the future of manufacturing.
With a commitment to quality and a focus on innovation, Deep Mould invites you to explore how our injection moulding tooling expertise can give your business a competitive edge in the ever-evolving market.