The Ultimate Guide to Wire Labler: Optimize Your Packaging Process
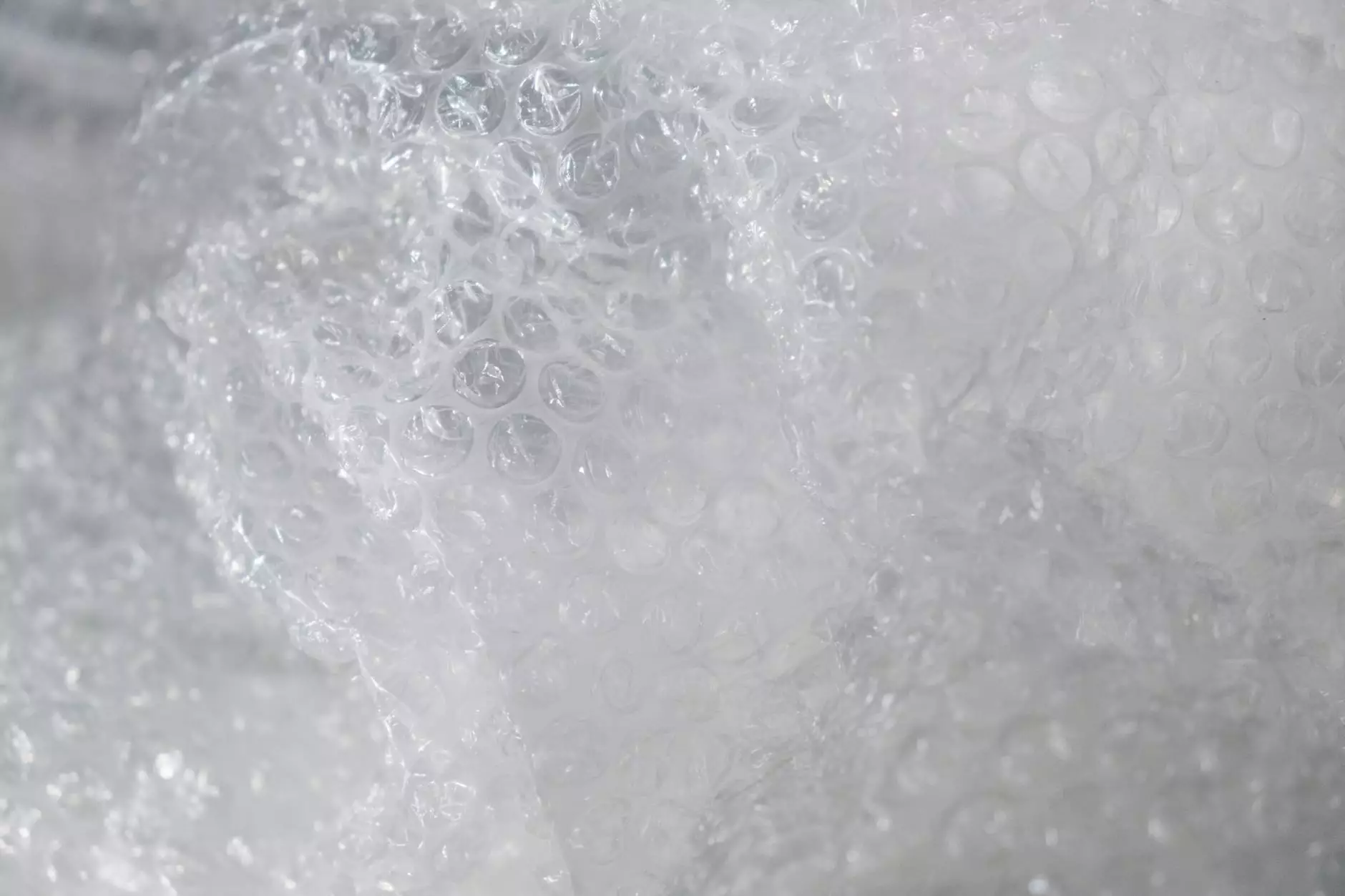
In the fast-paced world of manufacturing and packaging, efficiency and accuracy are paramount. One tool that has revolutionized packaging processes globally is the wire labler. This innovative machine simplifies the labeling process, ensuring that products are clearly marked and compliant with safety regulations. In this comprehensive guide, we will explore the various aspects of wire lablers, their advantages, and why they are an essential part of any packaging line.
Understanding Wire Lablers
A wire labler is a specialized piece of equipment designed to apply labels to wires, cables, and other small components. These machines can handle various label sizes and types, making them versatile tools in packaging industries ranging from electronics to automotive manufacturing. The efficiency of wire lablers lies in their ability to automate and streamline the labeling process, significantly reducing labor costs and minimizing errors.
The Types of Wire Lablers
There are several different types of wire lablers available in the market, each designed for specific applications. Understanding these can help businesses choose the right model for their needs:
- Desktop Wire Lablers: Ideal for small production runs, these compact machines can handle various labeling jobs without requiring significant floor space.
- Automated Wire Lablers: Designed for high-volume production, these machines integrate into larger manufacturing lines, working seamlessly with other equipment.
- Handheld Wire Lablers: Perfect for smaller tasks or mobile operations, these devices offer flexibility and portability without sacrificing efficiency.
- Integrated Labeling Systems: These systems combine labeling with other processes, such as printing or sorting, to further enhance productivity.
The Importance of Labeling in Manufacturing
Labeling in manufacturing serves several critical functions:
- Compliance: Proper labeling ensures that products meet industry regulations and safety standards.
- Branding: Labels are an opportunity for companies to showcase their brand, providing essential information to customers.
- Traceability: Accurate labels enable the tracking of products through the supply chain, essential for quality control and recalls.
- Information Dissemination: Labels provide necessary information about the product, including usage instructions, warnings, and specifications.
How Wire Lablers Enhance Your Packaging Process
Incorporating a wire labler into your packaging process offers numerous benefits:
1. Increased Efficiency
Automating the labeling process with a wire labler significantly speeds up production times. Traditional labeling methods can be slow and labor-intensive, whereas automated machines can apply labels at high speeds without sacrificing accuracy.
2. Cost-Effectiveness
By reducing labor costs and minimizing label waste, wire lablers prove to be a wise investment. As these machines contribute to faster turnaround times and higher throughput, they also enhance overall profitability.
3. Improved Accuracy
Human error is a common issue in manual labeling processes. A wire labler ensures that each label is applied consistently and correctly, reducing the chance of mislabeling and ensuring product compliance.
4. Versatility
Wire lablers can handle various types of labels and conform to different shapes and sizes, making them versatile for many applications. This adaptability allows businesses to pivot quickly to meet changing market demands.
5. Enhanced Aesthetics
Well-labeled products enhance the overall aesthetic appeal and professionalism. A high-quality label can differentiate products in a competitive market, potentially increasing sales and customer satisfaction.
Choosing the Right Wire Labler for Your Business
When selecting a wire labler, it’s crucial to consider several key factors:
- Production Volume: Determine the volume of labels you need to apply. For high-volume production, an automated labler might be necessary.
- Label Types: Identify what types of labels you will use. Some machines are better suited for particular materials or sizes.
- Integration: Consider how the labler will fit into your existing production line. Will it work seamlessly with other equipment?
- Budget: Investing in a quality machine can pay off in the long run, but always compare costs and ROI to ensure it meets your financial goals.
Maintenance and Care of Your Wire Labler
To ensure longevity and optimal operation, proper maintenance of your wire labler is essential.
Regular Cleaning
Dust and debris can impair the machine’s performance, so regular cleaning is vital. Ensure that you follow the manufacturer's recommendations for cleaning intervals and procedures.
Check and Replace Labels
Monitoring the label supply is critical to avoid production downtime. Regularly check and replace labels according to use and machine specifications.
Routine Inspections
Conduct routine inspections for wear and tear on components. This proactive approach can help identify potential issues before they disrupt operations.
Consult the Manual
Always refer to the user manual for specific maintenance advice tailored to your particular wire labler model.
Conclusion: Investing in Efficiency with Wire Lablers
In today's highly competitive market, businesses must leverage every opportunity to enhance efficiency and accuracy in their production lines. The wire labler stands out as an indispensable tool that not only streamlines the labeling process but also contributes to better compliance, branding, and overall product quality. By investing in a quality wire labler from a reputable Packaging Equipment Manufacturer like Shineben, you can ensure that your labeling processes are efficient, precise, and adaptable to future needs. Elevate your packaging today and experience the transformational benefits of advanced labeling technology!
To learn more about optimizing your packaging processes with wire lablers, visit shineben.com and discover how you can enhance your production lines!