Enhancing Packaging Efficiency with Case Erector Bottom Sealers
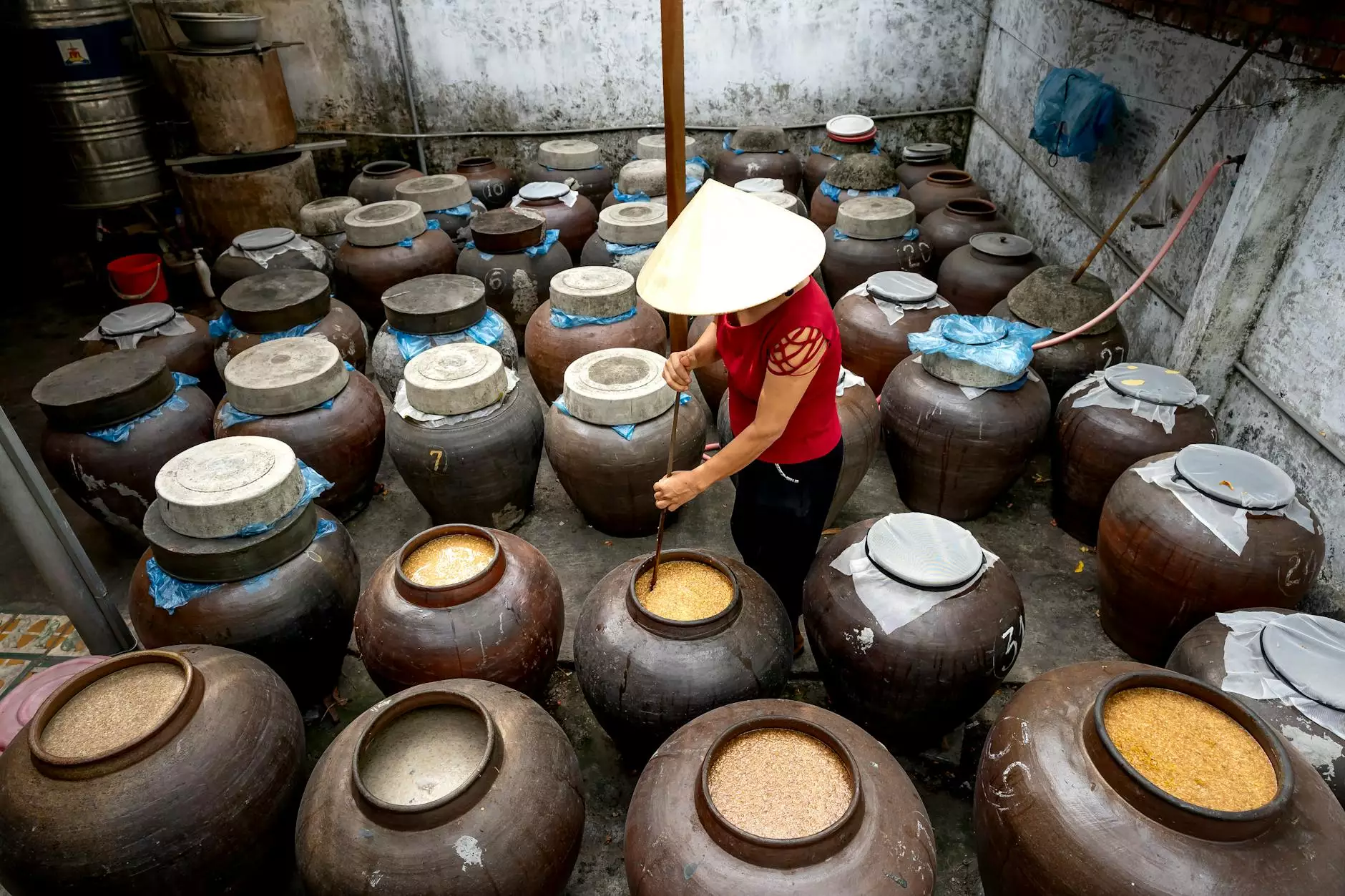
The packaging industry is a critical sector that contributes significantly to various businesses, ranging from food and beverage to e-commerce. One of the most revolutionary innovations in this industry is the case erector bottom sealer. This piece of equipment not only simplifies the packaging process but also ensures consistency and reliability in production. In this article, we will explore the importance of case erectors and bottom sealers, their functionalities, advantages, and how they can ultimately benefit your business operations.
Understanding Case Erectors and Bottom Sealers
A case erector is a machine that automatically forms and erects flat packed cartons into their required shape. This machinery plays a pivotal role in ensuring that boxes are ready for filling with products. On the other hand, a bottom sealer is responsible for sealing the bottom of these boxes securely, preventing any product spillage and ensuring the integrity of the packaged goods.
When these two systems work in unison, they significantly enhance the overall efficiency of packaging lines. Let’s dive deeper into their functionalities.
Functionality of Case Erectors
The primary function of a case erector is to take flat boxes, typically stored in a compact form, and convert them into three-dimensional boxes ready for products. Here’s how they operate:
- Box Orientation: The machine aligns the boxes in a specific direction.
- Box Formation: The flat box is pushed into a forming device, folding along pre-creased lines.
- Box Erection: The machine erects the box into its final shape.
The Role of Bottom Sealers
A bottom sealer follows the case erecting process, providing an essential sealing mechanism to the base of the boxes. The sealing can be achieved through various methods, including:
- Hot Melt Adhesives: These are commonly used for their strength and effectiveness in ensuring the base stays intact.
- Tape Sealing: An economical option that uses adhesive tape to secure the bottom of the box.
- Plastic Strapping: This method provides added security, especially for heavier packages.
Importance of Using Case Erector Bottom Sealers
Integrating case erector bottom sealers into your packaging process offers several advantages, including:
1. Increased Efficiency
Automated packaging systems such as case erectors and bottom sealers drastically reduce manual labor. This leads to faster production times, allowing businesses to meet consumer demands swiftly.
2. Cost-Effectiveness
While the initial investment in quality packaging equipment can be substantial, the long-term savings achieved through automation and reduced material waste are significant. Efficient sealing ensures that packaging materials are used judiciously, reducing overall costs.
3. Improved Product Integrity
With reliable bottom sealing, products are better protected during storage and transportation. This reduces damage and ensures that the products reach consumers in perfect condition.
4. Enhanced Flexibility
Many modern case erector bottom sealers can be adjusted to accommodate a variety of box sizes and shapes. This flexibility allows businesses to adapt quickly to changing product lines and market demands.
Types of Case Erector Bottom Sealers
When considering a case erector bottom sealer, it’s important to choose the right type for your specific needs. Below are some of the most common types:
1. Semi-Automatic Case Erector Bottom Sealers
These require some manual operation but still save a considerable amount of time. Operators typically load the boxes and activate the sealing process, making the system ideal for businesses with lower volume needs.
2. Fully Automatic Case Erector Bottom Sealers
Designed for high-volume production lines, these machines automatically erect, fill, and seal cases with minimal human intervention. They are equipped with sensors and actuators to streamline the entire process.
3. Robotic Case Erectors
Incorporating advanced technology, robotic case erectors can handle complex operations with precision. They are particularly useful in highly specialized production lines, offering high flexibility and efficiency.
Best Practices for Implementing Case Erector Bottom Sealers
To maximize the benefits of case erector bottom sealers, consider the following best practices:
1. Assess Your Production Needs
Understanding your production volume and type of product will help determine the right machinery for your business. This assessment should guide your purchase decisions.
2. Regular Maintenance
Implement a routine maintenance schedule to ensure your machines remain in peak condition. Regular checks can reduce downtime and prolong the life of your equipment.
3. Training Operators
Invest in comprehensive training for operators who will work with these machines. Well-trained staff can handle equipment properly, leading to fewer errors and an increase in overall efficiency.
4. Optimize Line Layout
The layout of your packaging line can significantly affect efficiency. Ensure that your case erector bottom sealer is strategically placed to minimize the distance between stations, thus speeding up the process.
Conclusion: The Future of Packaging with Case Erector Bottom Sealers
In the ever-evolving landscape of packaging, the introduction of case erector bottom sealers marks a significant milestone towards automation and efficiency. As businesses continue to strive for operational excellence, investing in high-quality packaging equipment is crucial.
At shineben.com, we understand the importance of reliable and technologically advanced packaging solutions. Our expertise in packaging equipment manufacturing ensures that you get the best equipment tailored to your specific needs.
As we move forward, companies that embrace these advancements will not only improve their bottom line but also create a more sustainable and efficient packaging process. Now is the time to consider how a case erector bottom sealer can transform your business operations and set you apart from the competition. Invest in your future today to remain ahead in the packaging industry.